What is Porosity in Welding: Comprehending Its Causes and Enhancing Your Skills
What is Porosity in Welding: Comprehending Its Causes and Enhancing Your Skills
Blog Article
The Science Behind Porosity: A Comprehensive Guide for Welders and Fabricators
Understanding the intricate systems behind porosity in welding is important for welders and makers aiming for flawless workmanship. From the structure of the base products to the ins and outs of the welding procedure itself, a plethora of variables conspire to either aggravate or ease the existence of porosity.
Understanding Porosity in Welding
FIRST SENTENCE:
Examination of porosity in welding reveals critical understandings into the honesty and quality of the weld joint. Porosity, identified by the visibility of dental caries or gaps within the weld metal, is a common problem in welding procedures. These gaps, if not effectively addressed, can endanger the structural integrity and mechanical residential or commercial properties of the weld, resulting in potential failures in the ended up item.

To identify and evaluate porosity, non-destructive testing techniques such as ultrasonic screening or X-ray assessment are usually employed. These techniques allow for the identification of internal defects without compromising the integrity of the weld. By analyzing the dimension, form, and distribution of porosity within a weld, welders can make informed choices to boost their welding processes and achieve sounder weld joints.
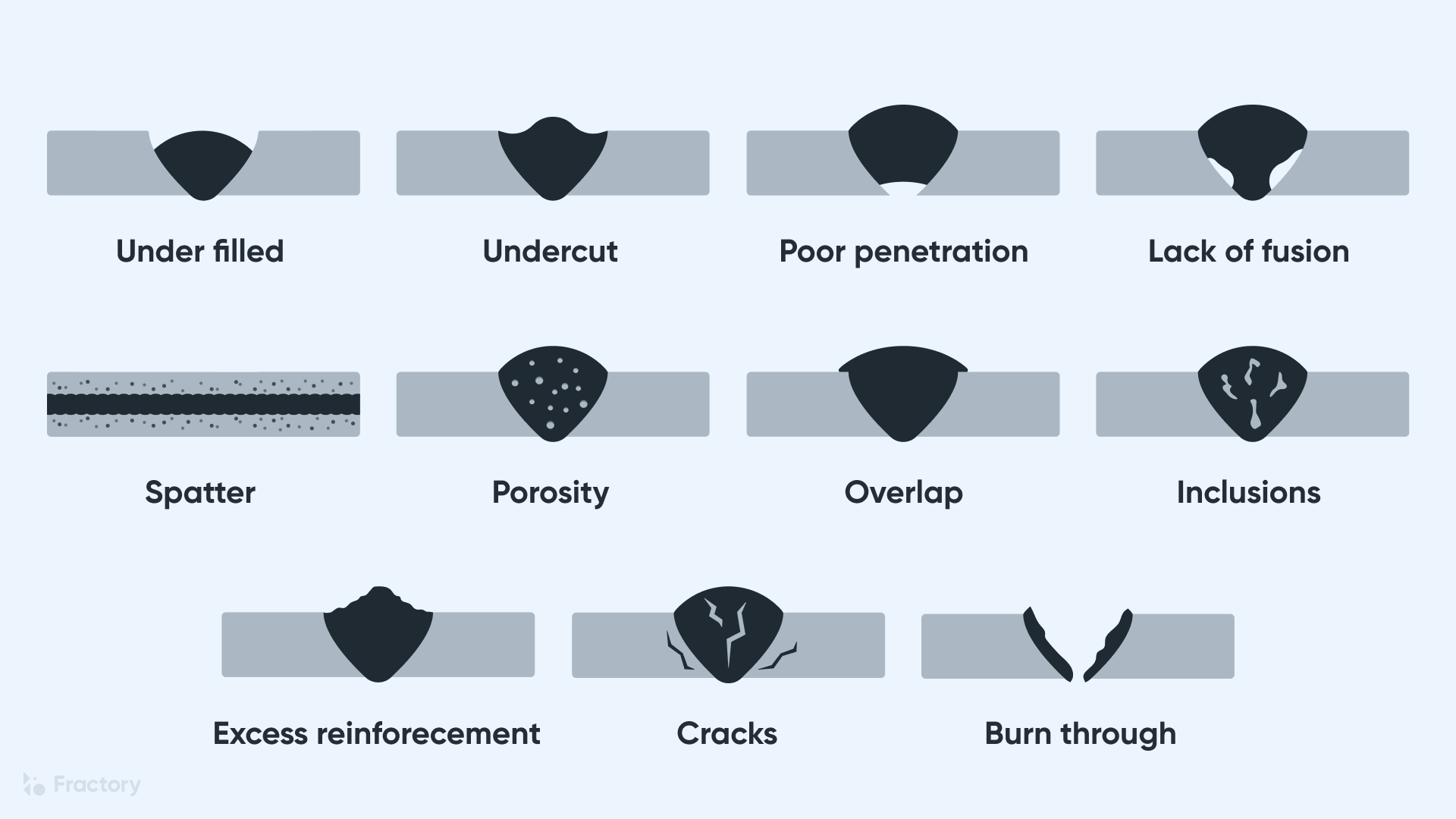
Elements Influencing Porosity Formation
The incident of porosity in welding is affected by a myriad of elements, varying from gas securing effectiveness to the ins and outs of welding parameter settings. Welding criteria, including voltage, existing, travel speed, and electrode kind, also effect porosity development. The welding method utilized, such as gas steel arc welding (GMAW) or shielded metal arc welding (SMAW), can influence porosity development due to variations in warm circulation and gas insurance coverage - What is Porosity.
Effects of Porosity on Weld Quality
Porosity development significantly compromises the architectural honesty and mechanical homes of bonded joints. When porosity exists in a weld, it produces spaces or dental caries within the material, lowering the here total strength of the joint. These voids act as tension concentration points, making the weld a lot more at risk to cracking and failure under tons. The existence of porosity additionally compromises the weld's resistance to rust, as the caught air or gases within the gaps can respond with the surrounding setting, bring about destruction with time. In addition, porosity can hinder the weld's ability to endure stress or effect, further endangering the total quality and reliability of the welded structure. In important applications additional hints such as aerospace, automotive, or structural buildings, where security and longevity are paramount, the detrimental results of porosity on weld high quality can have serious repercussions, highlighting the significance of reducing porosity through proper welding techniques and treatments.
Techniques to Decrease Porosity
Furthermore, making use of the appropriate welding criteria, such as the correct voltage, current, and travel speed, is essential in stopping porosity. Keeping a consistent arc size and angle throughout welding also helps reduce the probability of porosity.

Using the ideal welding strategy, such as back-stepping or employing a weaving activity, can likewise assist distribute warm evenly and reduce the possibilities of porosity formation. By carrying out these strategies, welders can effectively lessen porosity and create high-grade bonded joints.
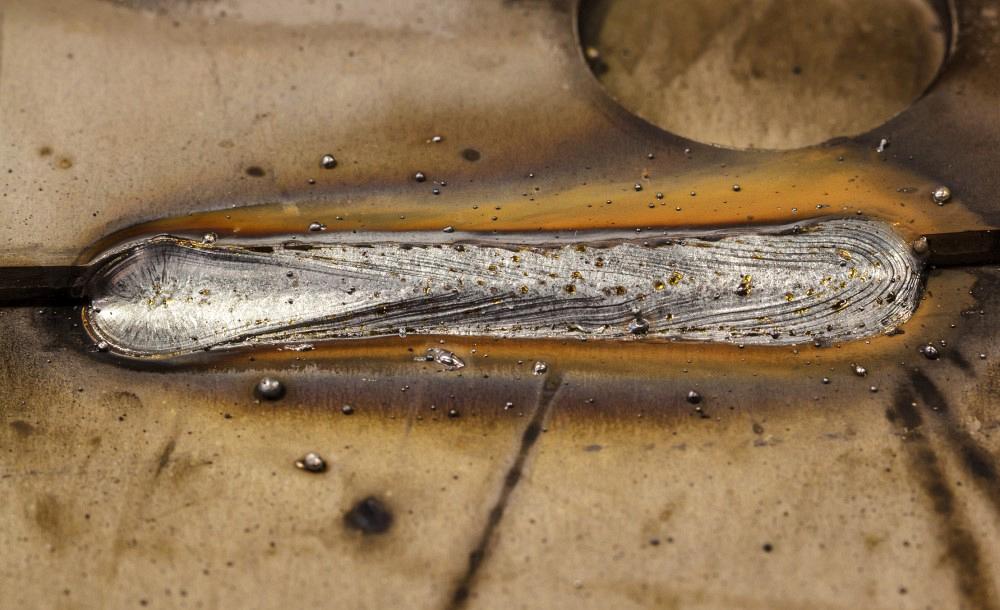
Advanced Solutions for Porosity Control
Implementing innovative modern technologies and ingenious approaches plays a pivotal function in accomplishing superior control over porosity in welding procedures. Furthermore, utilizing advanced welding techniques such as pulsed MIG welding or changed ambience welding can also aid alleviate porosity issues.
An additional sophisticated solution entails the usage of innovative welding tools. Making use of equipment with integrated attributes like waveform control and innovative power resources can boost weld top quality and reduce porosity risks. The implementation of automated welding systems with go to my blog precise control over parameters can considerably reduce porosity problems.
Additionally, incorporating advanced monitoring and inspection modern technologies such as real-time X-ray imaging or automated ultrasonic screening can assist in identifying porosity early in the welding procedure, permitting for instant restorative actions. Overall, incorporating these innovative options can considerably improve porosity control and enhance the total high quality of welded components.
Verdict
In verdict, comprehending the science behind porosity in welding is essential for welders and makers to create premium welds. By identifying the variables influencing porosity development and carrying out techniques to decrease it, welders can enhance the general weld quality. Advanced remedies for porosity control can additionally enhance the welding procedure and guarantee a solid and trustworthy weld. It is essential for welders to continually inform themselves on porosity and implement ideal practices to attain optimal outcomes.
Report this page